Technical Description
of the Conversion Kit
The MaxiCrown Conversion
Kit can be installed in most types of crowners and other sealing
machines with capacities up to 60 000 bottles per hour. Our reference
lists are covering more than 100 installations of the MaxiCrown
Conversion Kit. Our customers confirm equal reliability and efficiency
as for crown corks.
The Conversion Kit is
designed for efficient sealing of different types of ring pull caps
as MaxiCrown, Ring Crown and Rip Cap of sizes 26, 33, 38 and 42
mm. The MaxiCrown Conversion Kit has been carefully adapted to the
new MaxiCrown cap, made of aluminium
shell and PE ring (in Japan named Maxi-PGC), to provide optimal
sealing. The sealing machines are manufactured and supplied by us
(i.e., MaxiCrown Sealing Machines
AB in Sweden), that means by technicians with many years of
experience from this specific sealing technique.
Maxi
Crown
|
Rip
Cap
|
RingCrown
|
MaxiCap
|
|
|
|
|
|
|
|
26
mm
|
33
mm
|
38
mm
|
26
mm
|
42
mm
|
26
mm
|
26
mm
|
The Conversion Kit can
be installed either in lines at use with fillers or in new sealing
machines in cooperation with the actual manufacturer of filling
lines.
The optimal flexibility
and use of the whole filling line will be achieved by installing
the MaxiCrown Conversion Kit in a separate turret, allowing the
options of sealing glass bottles with crown corks and glass and
plastic bottles with MaxiCrown.
By specializing on MaxiCrown
sealing machines and making use of our long experience of this technique,
we are able to offer our customers competitive prices and secured
quality.
Conversion kit components
The MaxiCrown Conversion
Kit has 5 components:
1. Cap Transporter
Unit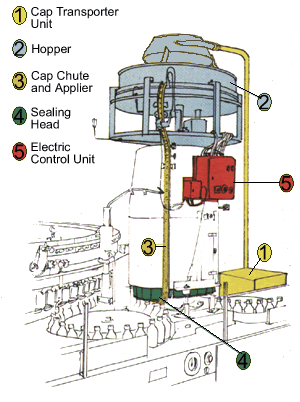
The caps are filled
into a storing bin and transported from there in pipes by air to
the hopper.
2. Hopper
The hopper
is positioned immediately
above the turret or on top of the crown cork hopper. Different sizes
of hoppers are offered according to required capacity.
3. Cap Chute and Applier
After orienting the caps in the hopper into correct positions, the
cap outlet is feeding the caps into the chute with the ring behind.
The cap chute
is kept full with caps. Each bottle passing the cap applier
is catching a cap with the bottle neck.
4. Sealing Head
The top pressure applied on the sealing
head forms the cap to the bottle neck. During the initial
phase of sealing the Maxi Crown cap is kept in position on the bottle
top and centered in the head by the inner plunger. By the final
downward movement of the sealing head the cap is formed to the bottle
neck. The cap fits tightly under the locking ring and provides good
sealing and reliability. The sealing heads are easily mounted on
existing sealing elements. Replacement heads are made available
for repair and cleaning, if requested.
5. Electric Control
Unit
The electric
control system is integrated with the main PLC of the filling
line, automatically stopping and starting the filling and the sealing
machines at any relevant disturbance. Sensors
are controlling and coordinating the feed of the caps. The electric
control system is installed in a Main Cabinet and an Operator's
Control Panel. These cabinets are made from stainless steel.
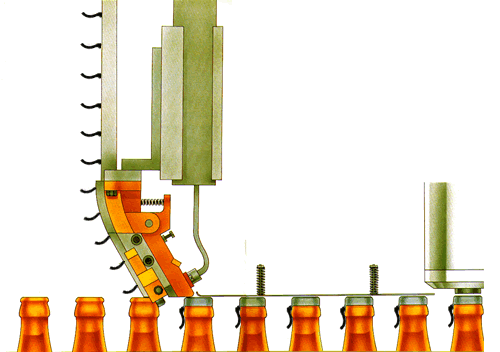 |
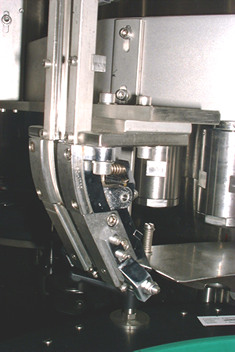 |
Cap
chute and cap applier
|
|
|
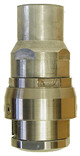 |
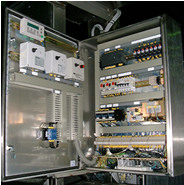 |
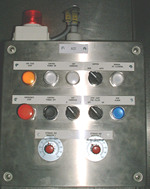 |
Hopper
|
Sealing
head glass bottles
|
Sealing
head plastic bottles
|
Electric
control Unit -
Main Cabinet
|
Electric
control Unit - Control Panel
|
|